添加傳統(tǒng)的阻燃劑工藝控制范圍更寬,更易達到較高要求的阻燃等級。國內市場上現(xiàn)有的阻燃膠衣樹脂,大多數是采用由HET酸或四溴苯酐等含鹵酸類合成的,反應型不飽和聚酯樹脂為基體配制的。一般添加型阻燃樹脂生產的玻璃鋼制品氧指數可達27,能滿足普通建筑防火要求,如要求更高,可再添加阻燃劑或選用反應型的阻燃樹脂。雖然它們有較滿意的阻燃性,但是耐候性能都不十分理想,在陽光下短時間的暴曬后就明顯變黃,很難達到生產白色或淺色玻璃鋼制品的要求。因此研究開發(fā)耐候性優(yōu)良、老化變黃度小的阻燃膠衣樹脂品種,是樹脂生產廠家和玻璃鋼生產企業(yè)十分關注的課題。
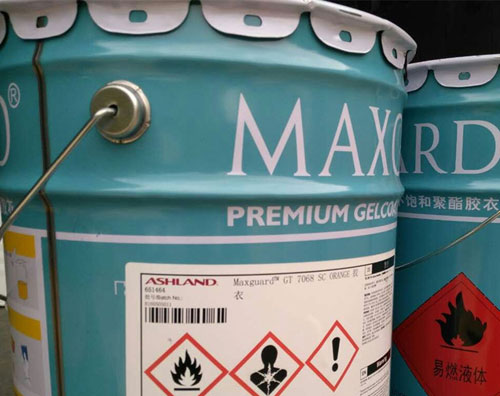
阻燃膠衣不飽和聚酯樹脂作為研究對象, 適當溫度下選用不同的促進劑-引發(fā)劑體系, 不同的濃度和配比, 進行了試驗。得到了以過氧化甲乙酮作為引發(fā)劑, 辛酸鈷作為促進劑的促進劑-引發(fā)劑系統(tǒng),對所合成的阻燃UPR具有較好的固化效果。促進劑和引發(fā)劑的用量分別是樹脂質量的1.2%和2.0%。合成無鹵阻燃UPR樹脂中的阻燃劑含量愈高阻燃效果越好;但阻燃劑的加入量對阻燃UPR產品的固化時間有很大的影響, 阻燃劑的加入量越大固化時間越長。當磷含量為3.5%時, 樹脂的固化溫度32℃,時間為10h。樹脂樣條的氧指數(LOI)為26.9。向該樹脂中加入適量的DMMP, 使阻燃膠衣樹脂的磷含量達5%時, 其LOI>28。